PIN TYPE EXTRUDERS
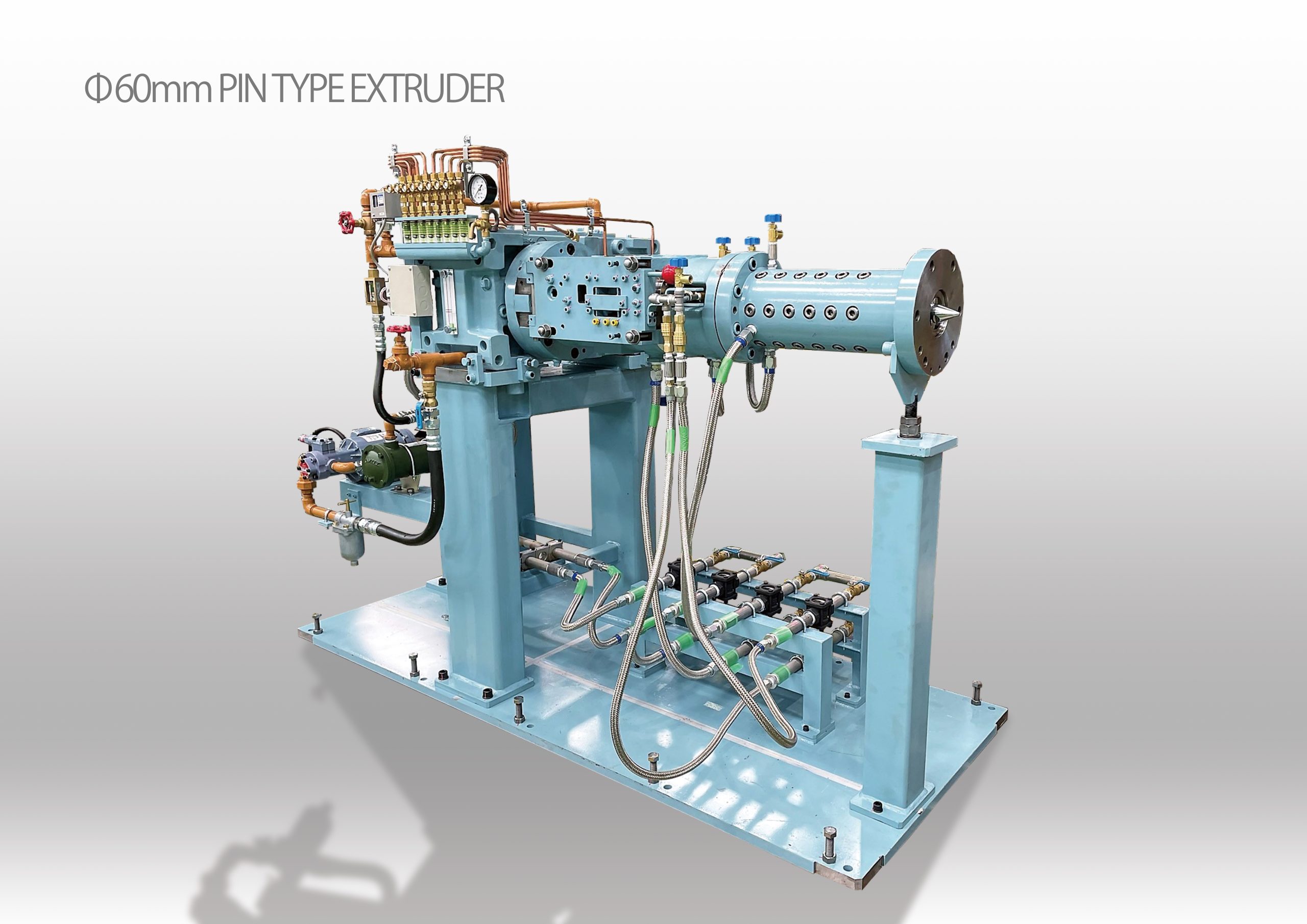
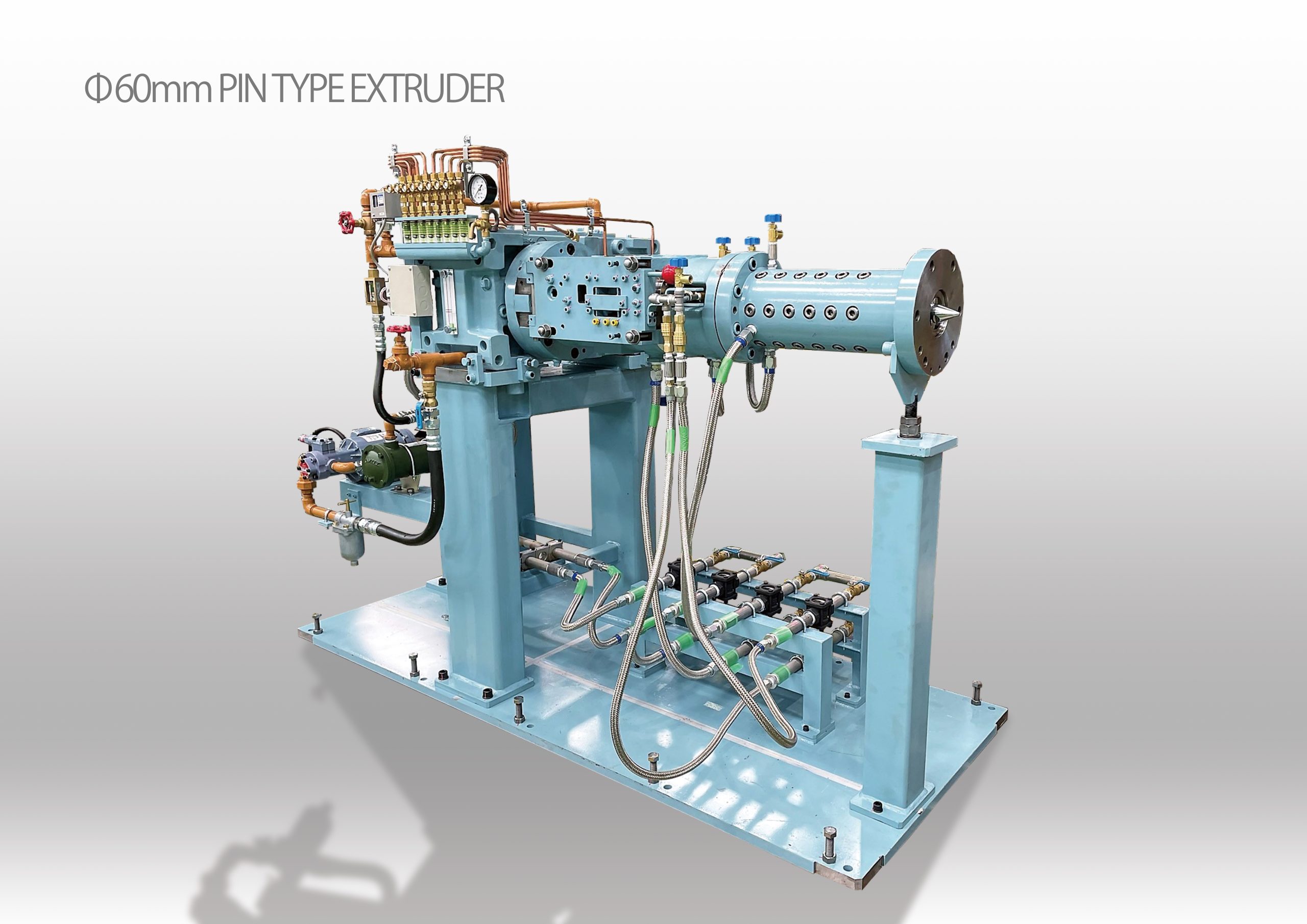
Overview
A mechanism of extruder works in this way: material rubber is charged at a root area of an elongate screw engaged in a cylindrical barrel, then plasticized by heat, kneaded and mixed while being transferred by screw rotation, and then pressurized against mouthpiece at the screw tip area and pushed out through it with a designed profile continuously.
We, Nakata Engineering, have manufactured the extruders majorly as a long-established maker of the rubber processing machinery and kept studying for further developments. We have provided to the market a “hot feed” extruder traditionally, then developed a “cold feed” type which can process material rubber at an ambient temperature, a “vent” type which can degas the trapped air in the processing rubber, and a “pin” type which realized higher output, in our long history. We are proud of our contribution to the advancement of the extrusion technology.
PIN TYPE EXTRUDERS
The pin type extruder incorporates a special design with 60 to 100 pins protruding from the cylinder wall toward the screw’s center. These pins enhance the mixing and dispersing of the rubber as it is kneaded between the screw and the cylinder, making the pin type extruder extremely flexible as a universal extruder that is applicable to many rubber compound formulations for diverse applications.
- 1) Applicable to a wide range of rubber compounds.
- 2) Pins enhance mixing to provide high uniformity in dispersion and plasticization of material.
- 3) Output is 20% to 60% higher than a conventional cold feed type extruder of the same size.
- 4) Rubber can be extruded at relatively low temperatures.
- 5) The low energy consumption (WH/KG) helps keep costs down, while conserving resources.
- 6) System is self-cleaning.
Specification
Related products
-
The most suitable equipment to produce rubber prof……
-
The most suitable equipment to produce rubber prof……
-
Variety of Our “Extruder” Peripheral Equipment
EXTRUDER EXCLUSIVE/PERIPHERAL EQUIPMENTS & DEV……
-
EXTRUDER EXCLUSIVE/PERIPHERAL EQUIPMENTS & DEV……